Part 21 Report - 1998-511
ACCESSION #: 9807150207
Ingersoll-Dresser Pump Company | Engineered Pump Group 942 Memorial Parkway Phillipsburg, NJ 08865 |
09 JY 98 | Fax # 301-816-5151 7 pages total sent |
US Nuclear Regulatory Commission
Document Control Desk
Washington, DC 20555
Attn.: Mr. Chancey Gould
Subject: 10CFR21 Reportability of a Potential Safety Hazard from broken Cast Iron Suction Heads in APKD Type Pumps
Dear Mr. Gould:
Per our telephone conversation this afternoon, Ingersoll-Dresser Pump Company is hereby notifying the NRC about a potential safety hazard from potential breakage of cast iron suction heads in APKD type pumps located at seven (7) different Nuclear sites.
Enclosed please find the engineering background, evaluation, conclusions, recommendations, typical component sketch, and a listing of the utilities, sites, pump types, order numbers, quantities and pump serial numbers that may be affected.
If you have any questions from an engineering standpoint, please call Bob Cornman at (908) 859-7256, and for quality control issues call me at (908) 859-7298.
| Sincerely yours, R. A. Hendricks Quality Assurance Manager |
RAH:sla
CC: | R. Rajeski | V. P. and Gen. Mgr. Engineered Pump Group |
W. Ord | President Engineered Pump Group |
R. Cornman | IDP - PE |
Enclosures
Ingersoll-Rand | Pacific | Worthington | Pleuger | Scienco | Jeumont-Schneider Pumps |
The purpose of this letter is to update the NRC on the Ingersoll-Dresser Pump evaluation of cast iron suction head damage experienced by one utility on Residual Heat Removal (RHR) pumps manufactured by Ingersoll-Rand Company. These pumps are of the model APKD designation and were manufactured in the mid 1970's.
BACKGROUND
The suction head (part number 360 as shown on Figure 1) is a cast, structural component that holds a bearing located below the double suction first stage impeller on the APKD type pumps (refer to Figure 1). The bearing holder is connected to the outer portion of the suction head with three or four support ribs depending on the pump designation. The suction heads were made from cast iron.
In addition to RHR applications, APKD type pumps in several different sizes have been supplied for Low Pressure Core Spray, and High Pressure Core Spray applications. Figure 2 contains a listing of the APKD type pumps supplied for various applications.
The problem was initially noted at the PECO Energy Limerick Unit #1 Nuclear Power Plant in May 1998. While investigating clogging of the #2 Jet pump, a piece of metal was found inside of the reactor vessel which ultimately was traced to the 1B RHR pump. A visual inspection (horoscope) of the 1B RHR pump revealed that a portion of the suction head was missing.
OBSERVATIONS
After a careful review of the information from the Limerick site and the inspection of the 1A & 1B RHR pumps, the following observations have been made:
1. | On the 1B pump, the lower bearing bracket broke off and became lodged in the inlet of the pump. This was evidenced by the wear pattern on the hub area of the bracket. In addition, the leading vane edges at the inlet of the lower eye of the first stage impeller had damage that appears to have been caused by contact with a rib of the bracket. |
2. | All bearings (except for the damaged suction head bearing) and impeller to casing wear ring clearances were measured and found to be within tolerance. |
3. | Overall, the 1B RHR pump was found to be in good condition. Two minor indications found on the #1 & #3 outer casing vanes required minor work to blend by hand grinding. |
4. | The inspection of the 1A RHR pump revealed that the suction head of the 1A RHR pump was found intact. The suction head journal sleeve (part number 135A on Figure 1) was found to have moved approximately one quarter inch relative to the shaft. |
5. | Inspections of both the 1B & 1A RHR pumps indicate that downward movement of the suction head journal sleeve was wearing the key (part number 291 on Figure 1) installed to prevent rotation between the journal sleeve and the shaft. |
6. | The 1B RHR pump is of a similar design to the 1A Condensate pump which experienced a suction head failure in December of 1997. Information obtained from the plant suggests that the 1A Condensate pump may have been operated in a failed suction head condition with no noticeable degradation in performance for 12 to 18 months of continuous service. |
7. | A suction head failure as observed on the 1B RHR pump would be expected to change the vibration response of the pump; however, the vibration data for the 1B RHR pump and the 1A Condensate pump did not indicate an abnormal vibration response during normal operation. |
8. | The 1B RHR pump had passed all of its surveillance test requirements. |
9. | A mathematical analysis performed on the suction head, taking into account the expected mechanical, hydraulic, and thermal effects, did not indicate sufficient loading to cause the failure. |
CONCLUSIONS
The failure mode of this suction head appears to start with the migration of the suction head journal sleeve along the lower end of the pump shaft due to wear of the key that holds the sleeve in place. This is a result of the accumulated operating time on the pump. Once the sleeve is detached from the shaft, it is able to move in the lower portion of the pump and strike the suction head causing breakage of the support rib.
As demonstrated by the experience with the 1A Condensate pump, a pump can operate without a measurable degradation in performance for a period of time with a suction head failure. Gradually, a decline in performance would be observed over time. The expected trends that would result from a pump operating in this degraded condition would be a deterioration in the head/flow characteristics of the pump and a corresponding increase in vibration.
The failure of the suction head would not likely result in an immediate pump parameter change unless a portion of the suction head became lodged in one of the pump impellers. It must be noted that at the Limerick 1 site, both the 1B RHR pump and the 1A Condensate pump passed pieces of broken suction head rib without affecting the pump operation.
RECOMMENDATIONS
Ingersoll-Dresser Pump's recommended action plan for those pumps listed in Figure 2 is as follows:
1. | Inspect pumps at reasonable intervals for possible damage to the suction head, suction head journal sleeve, and retaining key. |
2. | If the surveillance testing has shown a recent degradation in the hydraulic performance of the pump or a recent change in the pump vibration, then the pump should be inspected immediately for possible damage to the suction head/suction head journal sleeve. |
3. | When required, a replacement suction head manufactured from carbon steel with additional rib stiffening and a suction head journal sleeve with improved axial positioning should be installed. |
4. | Monitor vibration on the pump shaft and motor housing and increase the frequency of the surveillance testing until an inspection of the suction head, suction head journal sleeve, and retaining key can be completed. |
rec98030B
FIGURE 1 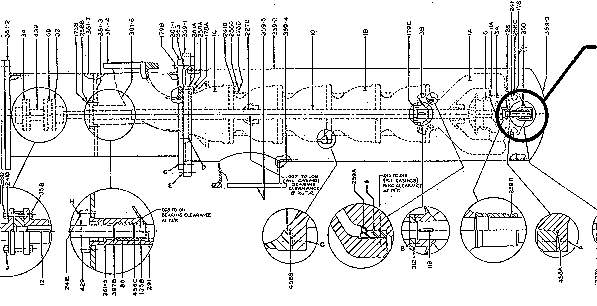
FIGURE 2 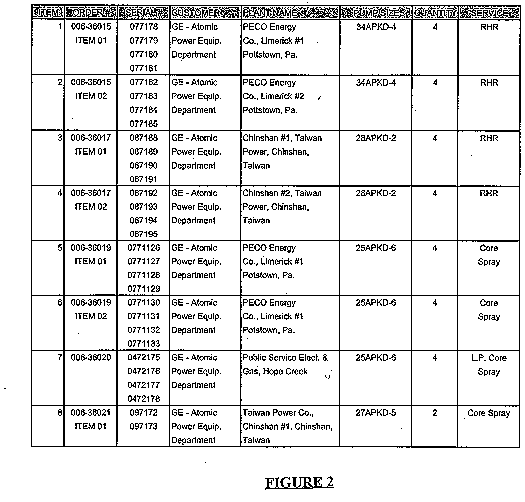
FIGURE 3 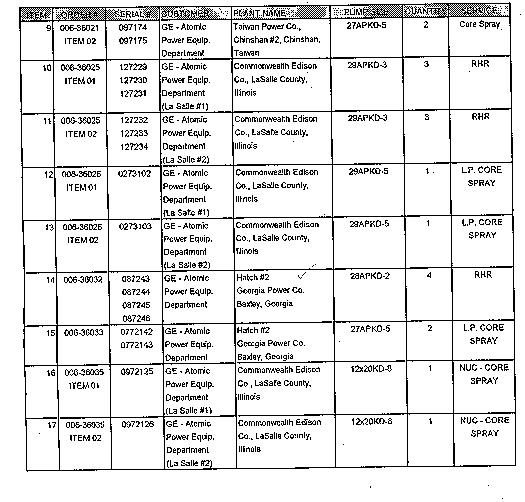
FIGURE 4 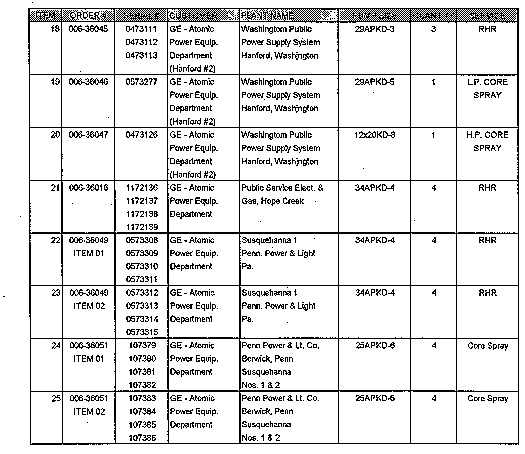
*** END OF DOCUMENT ***
Page Last Reviewed/Updated Wednesday, March 24, 2021